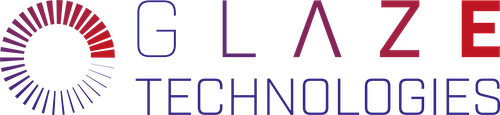
Non-destructive mapping of a steel carcass structure enclosed in a thick polymer layer — in collaboration with NOV Flexibles
Flexible offshorepipes must endure immense external pressure while maintaining flexibility, making precise control and accurate knowledge during production critical to ensure optimal performance. Deviations in manufacturing can lead to the pipe being out-of-specifications. One key parameter, the "pitch" of the innermost steel carcass, measures the distance between structural repetitions along the pipe's length. This pitch must remain within a specific range to maintain the necessary collapse strength and flexibility of the carcass. Traditionally, monitoring pitch variations during production has not been possible once the polymer pressure sheath has been extruded on top of the carcass.
GLAZE Technologies' device and analysis software enables non-destructive detection of the carcass pitch directly through the polymer pressure sheath. This method has been rigorously validated by comparing our measurements with those obtained from destructive tests, where the polymer pressure sheath was removed and a manual calliper was used to measure the exposed carcass pitches, confirming the accuracy and reliability of our approach.
The metal carcass acts as a near perfect mirror for our terahertz pulse, reflecting a strong signal even after penetrating approximately 8-10 mm of polymer. The arrival time of the reflected pulse changes along the structure of the carcass. By tracking the arrival time of the reflection as we scan along the pipe, we can map out the corrugated structure of the carcass surface. A subsequent analysis of the structure allows for automatic extraction of the pitch distance, either as a single pitch or an average over several pitches for better statistics.
The measurements were performed on a stationary cut-out segment of a flexible pipe at NOVs facilities. Using a linear stage, we conducted a line scan along the length of the pipe in sections of 30 cm.
By tracking the distance to the metal carcass at the point of measurement along the pipe, a topological profile can be recreated. We adjust for misalignment between thestage and the pipe and apply smoothing. A repeating and identifiable feature is chosen and the distance between said feature can be calculated. In the plot below, the result of the analysis is shown with annotated individual and averaged pitch.The resulting pitch, for this section of the pipe, ranges between 37.4 mm and 38.4mm. The spatial resolution is limited by the scanning step size used and not by GLAZE's technology.