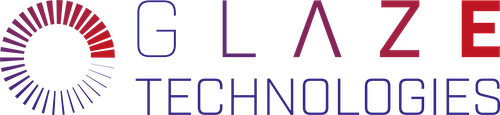
Enhancing performance and efficiency with precise thickness measurements of individual coating layers
In the maritime industry, the integrity and performance of multi-layered coating systems are critical for protecting vessels from corrosion and biofouling. Among these, the anti-fouling layer plays a significant role in reducing hull drag and improving fuel efficiency. Accurate measurement of these coating layers ensures optimal performance and cost-effectiveness. Existing solutions are mostly either destructive or cannot distinguish between individual coating layers.
GLAZE Technologies’ offers a state-of-the-art solution for non-destructive thickness measurements, providing reliable data to maintain the efficiency of these coatings. Our solution provides thickness information about each individual coating layer in a single measurement. Our system can be handheld and portable allowing for measurements in the field.
The terahertz lightwaves are directed towards the coating system, and the reflected signal is detected. At each interface between the coatings, the signal will be partly transmitted and partly reflected. The signal from each interface carries information about the material itself along with information about the travel time from emitter to detector. The difference in arrival time at the detector between interface reflections reveals the thickness of each layer.
In some cases, a so-called time-of-flight analysis can reveal the thicknesses simply by measuring the difference in arrival time between reflected signals. In case of maritime coating, many layers are so thin that the reflected signals are overlapping in time such that separating arrival times is not feasible. In that case we utilize a method where we compare the signal to a reference signal and calculate what the material characteristics should be for the sample signal to have the specific signatures it has. The whole process is done in a few seconds.
In the plot below, the accumulated thickness is plotted with the individual layer thicknesses annotated on each layer. Each set of values at a specific position on the sample is from a single measurement where the thicknesses has been retrieved with the before-mentioned algorithm. The total thickness and individual thicknesses correspond very well with the expected thicknesses of the sample manufacturer.
The method can easily be extended to 2D scans to create thickness maps of areas of interest. With our solution, rich quality testing is possible to ensure correct thicknesses after application or later testing ensuring the continued integrity of the coating system and that sufficient thickness of the outermost layer remains after extended periods of operation.