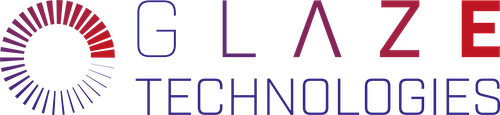
Ensuring optimal curing and layer application for enhanced durability
In the maritime industry, the proper curing of coatings is critical to ensure the longevity and performance of protective layers on ships and marine structures. Incomplete or incorrect curing can lead to premature failure, increasing maintenance costs and risking structural integrity. GLAZE Technologies demonstrates that terahertz lightwaves can be used to precisely monitor the curing state of maritime coatings. This technology can provide real-time feedback, ensuring each layer is fully cured before the next application, resulting in optimal protection and cost savings. Current methods are mostly destructive or relies look-up tables with variables as temperature and humidity.
By monitoring the curing directly, we can provide insight into the curing process both to make sure the coating is fully cured and also to avoid unnecessary waiting time before applying the next layer.
The terahertz lightwaves are directed towards the wet coating and reflected back to the emitter. As the coating cures, the chemical composition changes leading to a change in the refractive index. The refractive index is an inherent optical characteristic of a material that affects the transmission and reflection coefficient as well as the speed of light within the material.
By monitoring various coatings during the curing process in a controlled setting, a profile of the curing progress can be constructed from the change in refractive index. From that profile it is possible to make predictions on a similar coating either by a single measurement accompanied by knowledge of other parameters like temperature and humidity — or by a small series of measurements alone, where the trend can be matched to the known profile.
The Carmen device by GLAZE Technologies is portable and can be operated handheld, allowing for measurements of coatings in dry dock during the curing process.
The figure below shows the time development of the terahertz lightwave signal as the coating cures. The measurements where taken over a 8 hour period every 10 minutes.
In the top plot, we see all the individually recorded pulses where dark blue is the start of the experiment (a few minutes after application) and light red is at the end of the experiment. The x-axis represent the arrival time of the emitted and reflected terahertz lightwave at the detector and y-axis represents the amplitude. We clearly see a reflection from the coating surface and the metal substrate.
In the bottom plot, we track the peak value of both coating and metal reflection over time. We see a clear development that seems to be reach a steady state at around 4 hours, halfway through the experiment. But towards the end, there's still a development although subtle. In the wet paint, there are two main processes that changes the material characteristics: drying and curing. Drying is the evaporation of the solvent, which happens relatively fast, whereas the curing is a longer chemical process. What we see might be a mixture of those two processes, although more experiments are needed to fully understand how the signal is affected by the individual processes.
It's important to note, that we have conducted extensive tests of the amplitude drift in the Carmen system, and it is significantly smaller than the change in the figures below. We can therefore confidently contribute the changes in the signal to the changes in the coating.
Other similar experiments with different types of coatings have shown clear time development, but with different characteristics depending on the type. Therefore an initial profiling is needed for a specific coating before the system is ready to perform direct quantification of the curing process.